DFG AMECOMP
- Contact:
- Funding:
DFG - Deutsche Forschungsgemeinschaft
ANR - Agence Nationale de la Recherche - Partner:
KIT: Institut für Fahrzeugsystemtechnik, Institutsteil Leichtbau (FAST-LB)
Institut National des Sciences Appliquées de Lyon (INSA Lyon): Contact and Structural Mechanics Laboratory (LaMCoS)
- Startdate:
06/2020
- Enddate:
12/2023
AMECOMP – Composite forming simulation for non-crimp fabrics based on generalized continuum approaches
↵
AMECOMP is an international collaborative research project of the German Karlsruhe Institute of Technology (KIT) and the French National Institute of Applied Sciences of Lyon (INSA), funded by the German Research Foundation (DFG) and the French National Research Agency (ANR).
KIT, Germany | INSA Lyon, France | |
Project Coordinators | Prof. Dr.-Ing. Luise Kärger |
Dr.-Ing. Naim Naouar Prof. Dr. Philippe Boisse |
Contact | luise.kaerger∂kit.edu https://www.fast.kit.edu/lbt |
- The full project report is published under https://doi.org/10.34657/13755
- Citation: B. Schäfer, L. Kärger, N. Naouar, R. Zheng. Composite forming simulation for non-crimp fabrics based on generalized continuum approaches – AMECOMP : Abschlussbericht / Final project report (DFG 431354059 / ANR-19-CE06-0031). Hannover : Technische Informationsbibliothek, 2024. DOI: 10.34657/13755
Consolidated summary
"Detailed mesoscopic and efficient macroscopic models for forming of non-crimp fabrics"
Composite forming simulation for non-crimped fabrics based on generalized continuum approaches
Continuously carbon fiber reinforced composites are increasingly used for structural applications in various fields of engineering due to their excellent weight-specific mechanical properties. Non-crimp-fabrics (NCF) provide the highest lightweight potential as reinforcement for the composite due to their straight fibers, compared to woven fabrics with undulated fibers. NCFs are made of one (UD-NCF), two (Biax-NCF) or more directions of fibers linked together with a polymer stitching in specific patterns. The deformation behavior of NCFs is challenging due to the interaction between the fibers and the stitching, which also results in a higher susceptibility to forming effects such as roving slippage, fiber waviness and gapping compared to woven fabrics.
The aim of the AMECOMP project was to improve the understanding of the forming behavior of NCFs and to develop suitable simulation models to broaden the range of potential applications. Mesoscopic models that accurately describe the architecture of the NCF were developed for virtual material characterization and detailed analysis of forming defects in critical areas. Macroscopic models that describe the relevant deformation mechanisms of NCF in a homogenized way were developed for efficient analysis of large components and multi-layer stacks.
Experimental characterization and modeling of textiles at meso and macro scale and exploration of generalized continuum mechanics approaches
A comprehensive characterization and understanding of the forming behavior is essential to develop suitable modeling approaches. Experimental tests on isolated fiber rovings and on the stitching were combined with computer tomography measurements of the textile architecture to develop an accurate mesoscopic model. Experimental coupon tests for the membrane, bending, out-of-plane compaction and friction behavior were conducted to determine the homogenized material properties for a macroscopic model. Approaches based on generalized continuum mechanics were explored for both models to improve their accuracy and to overcome the limitations of conventional approaches based on Cauchy mechanics, which cannot simultaneously express the bending stiffness of the single fibers (microscopic stiffness) and the slippage between the fibers. The reliability and accuracy of the mesoscopic as well as macroscopic model were validated by comparison to experimental forming tests of different geometries, initial fiber orientations and layup configurations. Optical measurement techniques were used to ensure quantitative agreement of the final fiber orientation, strain distributions and gapping.
Major project results
- Initiation of a partnership and knowledge exchange between the French partner at INSA Lyon and the German partner at KIT Karlsruhe.
- A comprehensive experimental database was established for the different deformation mechanisms and forming behavior of a commercially relevant UD- and Biax-NCF.
- A parametric mesoscopic Finite-Element model of Biax-NCF was developed based on the real geometry from tomography results. The model can be easily adjusted for new fabric architectures and incorporates the roving bending stiffness based on a superimposed beam element approach.
- A mesoscopic forming model for UD-NCF was developed with the ability to investigate local deformations such as slippage between fiber rovings and the formation of gapping.
- A macroscopic forming model for UD-NCF was developed based on a hyperelastic approach that accounts for superimposed shear, transverse tension and in-plane compression of the fiber rovings. The new model requires significantly fewer material parameters then existing approaches to simplify its parameterization and facilitate its transferability to other materials, as demonstrated for Biax-NCF.
- A three-dimensional solid-shell-element for Finite-Element forming simulations of textiles was developed, that accounts for a decoupled membrane and bending behavior of fibrous materials based on the idea of a second gradient approach. The new element formulation can account for out-of-plane compaction during forming to predict the final thickness and consequently fiber volume content, in contrast to existing approaches mainly based on two-dimensional formulations.
Scientific publications within the project
- 2 dissertations, one from each project partner
- 2 scientific papers in international peer-reviewed journals
- 2 scientific papers submitted to international peer-reviewed journals and under review at the end of the project
- 8 peer-reviewed conference papers with oral presentations at international conferences
- 1 conference paper without peer-review, with oral presentation at an international conference
Detailed project report
1. Brief summary
Non-crimp-fabrics (NCF) provide the highest lightweight potential as reinforcement for continuously fiber-reinforced composites due to their straight fibers, compared to woven fabrics with undulated fibers. NCFs are made of one (UD-NCF), two (Biax-NCF) or more directions of fibers linked together with a polymer stitching in specific patterns. The deformation behavior of NCFs is challenging due to the interaction between the fibers and the stitching, which also results in a higher susceptibility to forming effects such as roving slippage, fiber waviness and gapping compared to woven fabrics.
The aim of the AMECOMP project was to improve the understanding of the forming behavior of NCFs and to develop suitable simulation models to broaden the range of potential applications. Mesoscopic models that accurately describe the architecture of the NCF were developed for virtual material characterization and detailed analysis of forming defects in critical areas. Macroscopic models that describe the relevant deformation mechanisms of NCF in a homogenized way were developed for efficient analysis of large components and multi-layer stacks. Approaches based on generalized continuum mechanics were explored for both models to improve their accuracy and to overcome the limitations of conventional approaches based on Cauchy mechanics, which cannot simultaneously express the bending stiffness of the single fibers (microscopic stiffness) and the slippage between the fibers. The developments within the project improve the predictability of local forming effects like fiber waviness and gapping, as well as the global fiber orientations and fiber volume contents.
2. State of the Art, Challenges and Issues
The combination of three main research gaps constituted the motivation behind the AMECOMP project. First, despite the superior mechanical properties of NCFs, woven fabrics have often been the focus of research on experimental characterization and modeling in the context of forming due to their easier formability [1]. As a result, the deformation behavior of woven fabrics is well understood and many approaches for different weaving types have been identified. Most characterization setups are transferable to NCF, but the orientation and architecture of the stitching introduces additional influences that require further consideration. Mesoscopic models for woven fabrics have already been proposed with varying levels of detail, but for Biax-NCF [2] or UD-NCF [3] only models that are too simplified to investigate local effects such as gapping during forming have been presented. This also limits their usability to conduct virtual material characterization based purely on experimental tests on the fiber rovings and stitching, which would significantly reduce the necessary amount of test as successfully demonstrated for woven textiles. Macroscopic models for Biax-NCF have been proposed based on hypoelastic or hyperelastic approaches accounting for shear superimposed with stitching tension. However, all approaches for Biax-NCFs neglect intra-ply slippage between rovings and large tensile strains of the stitching, which are highly relevant mechanisms for UD-NCF during forming due to the lack of a second fiber direction. The model developed by Schirmaier et al. [4] at KIT was the only macroscopic model for UD-NCF at the beginning of the project. It can predict the global forming behavior (fiber orientation, preform contour, wrinkling), but requires a high number of material parameters and is unable to predict local effects like in-plane wrinkling or in-plane roving bending. Therefore, one objective of the AMECOMP project was the experimental investigation of NCFs with respect to the influence of the stitching on the mesoscopic and macroscopic deformation modes as well as the subsequent development of suitable modeling approaches for both scales.
The second research gap relates to the consideration of out-of-plane compaction during forming, which has a major impact on the fiber volume content in the final composite structure. The majority of macroscopic forming models are based on 2D shell elements and therefore are unable to describe out-of-plane compaction. The problem with the application of common 3D solid finite elements for forming simulation of composites is the occurrence of numerical locking phenomena, which cause the elements to have a too high bending stiffness [1]. An approach to solve these problems are so-called solid-shell elements, as demonstrated by Xiong et al. [5] at INSA for prepreg forming. However, no solid-shell element has been developed for forming simulations of UD- or Biax-NCF, which was the second objective of the AMECOMP project.
The third research gaps results from the limitations of Cauchy mechanics (1st displacement gradient), which is applied in most existing approaches for textile forming. The standard models of Cauchy mechanics are not sufficient to correctly describe the deformation of the fibrous reinforcements during their forming [6]. All phenomena related to the bending stiffness of fibers are not correctly modeled by a first gradient model and require the consideration of generalized continuum approaches that consider the 2nd gradient in hyperelastic models. In 2D element-based models, generalized continuum approaches are mainly necessary to account for the in-plane bending stiffness of the fibers, while the out-of-plane bending stiffness can be alternatively described by superimposing membrane and plate elements or utilizing neighboring elements [7]. In 3D element-based models for the rovings in mesoscopic approaches or solid-shell formulations for macroscopic approaches, generalized continuum approaches are necessary to describe the out-of-plane bending stiffness of the fibrous material correctly. Therefore, the third objective of the AMECOMP project was to explore the incorporation of generalized continuum approaches and their parameterization for all developed models.
3. Scientific and technical approach
To make the findings as transferable as possible for different textile architectures, both partners investigated the same commercially relevant NCFs with a similar tricot stitching pattern in a unidirectional (©UD300) and a balanced bidirectional (©MD600) architecture, produced from the same type of carbon fiber rovings (©Zoltek Panex PX35 50K). Based on the identified research gaps, the project was structured into six tasks. Task 1 focused on the experimental characterization of a UD- and a Biax-NCF with existing and partly adapted test setups at both partners. Characterization of the isolated rovings and stitching was conducted at INSA as a basis for the mesoscopic modeling. Characterization of the membrane, bending, compaction and friction behavior of larger coupon specimen was conducted at KIT to determine the homogenized properties for the macroscopic modeling as well as the initial validation of the mesoscopic model. Emphasis was placed on the membrane behavior to identify the necessary parameters for generalized continuum approaches by measuring the in-plane curvature of fibers. Task 2 focused on the development of a mesoscopic model to analyze the occurrence of local defects like gapping and enable virtual material characterization to identify the parameters for the macroscopic approach (1st and 2nd gradient). Previous work done at INSA on meso-modeling of fabrics and their model generation based on X-ray computer tomography (CT) measurements was used as a starting point. Task 3 focused on the experimental analysis of the forming behavior of UD- and Biax-NCF on part level for validation of the developed models, by measuring the mesoscopic effects like fiber orientation, fiber volume content and gapping for different formed geometries available at INSA. Task 4 focused on the development of a macroscopic model for NCFs and was split according to the preliminary work with a focus on Biax-NCF at INSA and UD-NCF at KIT. In addition, a solid-shell element suited for generalized continuum approaches and modeling of out-of-plane compaction during textile forming was developed at KIT. Task 5 focused on the validation of the developed modeling approaches based on the experimental forming tests of Task 3. Additionally, the advantages and benefits of generalized continuum approaches were evaluated by comparison to conventional Cauchy based approaches. Task 6 focused on investigating NCF recycling opportunities to meet the growing environmental demands of product development.
4. Results
Task 1: Experimental characterization
Mesoscopic: X-ray tomography was used to measure the geometric parameters of the warp and weft rovings, while the stitches were described explicitly from the knit pattern [8]. Appropriate experimental tests on individual rovings and stitching yarns were designed and conducted to obtain material input data. In these tests, the individual rovings and stitches are isolated from the Biax- NCF reinforcements by cutting the stitch loop connections.
The elongation behavior is directly identified from tensile tests of a single roving. The compaction and distortion behavior are characterized with compression tests conducted on single rovings. Concerning the longitudinal shear, the uniaxial tension test usually performed for woven fabrics were insufficient, since NCFs have no crimp. Thus, a new shear test on single rovings was developed and conducted at INSA [8]. Cantilever bending tests were conducted to characterize the out-of-plane bending stiffness of fiber rovings and stitching.
Macroscopic: In the systematic characterization of all intra-ply (i.e. membrane [9], bending [10] and compaction [11]) and inter-ply (i.e. friction [12]) mechanisms at KIT, the specific requirement of both NCFs and the resulting trends due to the influence of the stitching were identified. From a macroscopic perspective, the Biax-NCF often behaved similarly to a woven fabric as the stitching couples the deformation of both fiber layers. Instances of observed roving slippage and gapping were very limited and mainly mesoscopic. The UD-NCF exhibited some similar phenomena but also fundamental differences to the Biax-NCF, especially for the membrane and bending behavior. A strongly anisotropic and asymmetric behavior was observed, because the transverse behavior is determined by the stitching instead of a second fiber orientation. Additionally, a new method to measure the in-plane roving curvature of both textiles during off-axis tension tests with DIC was developed [9]. This provided a quantitative measure of the size and magnitude of transition zones that can be used to parametrize generalized continua approaches and so far had only been studied qualitatively in literature.
Task 2: Mesoscopic modeling
The method development for mesoscopic modeling approaches was the main focus at INSA. The CT measurements were combined with a geometrical approach to create an accurate 3D model of the Biax-NCF [8]. A purely CT-based approach was found insufficient for NCFs due to the challenges in separating the stitching and rovings in CT. The geometrical approach applies a parametrical description of the geometrical features of the Biax-NCF and enables a future transfer of the approach for arbitrary textile architectures (initial roving widths, stitching pattern). The roving is considered as a 3D solid with a hyperelastic anisotropic material model for its tension, compaction, and shear behavior, while its bending behavior is incorporated using an additional embedded beam element as substitute for a 2nd gradient approach. The stitching is modeled by beam finite elements. A pseudo thermal pretension step is developed to reproduce the stitch knitting process before numerical study and simulate the interaction between rovings and stitching.
The in-plane behavior was validated by shear simulations of a RUC (Representative Unit Cell) and bias-extension tests with good agreement for the roving width, gap development, and inter-layer roving slippage [8]. The good agreement with experimental shear forces, based on the parameters obtained only from isolated roving and stitching tests, demonstrates the potential of this model for virtual material characterization. The embedded beam element improves the representation of the out-of-plane behavior in virtual three-point bending tests.
The general transferability of the approach to UD-NCF was demonstrated in a student’s bachelor thesis at KIT [13], but not further pursued as the macroscopic approach in Task 4 could be sufficiently parameterized based on the macroscopic characterization from Task 1.
Task 3: Experimental analysis on part level
The forming behavior of the UD- and Biax-NCF were investigated for different double-curved punch shapes (hemisphere, tetrahedron, square box) at INSA with a focus on the membrane deformation. Transparent tools were combined with an open-source DIC algorithm from KIT to measure the resulting contours, macroscopic strains and observed defects [14]. For the balanced Biax-NCF, similar to Task 1, a behavior resembling that of woven fabrics was observed with a shear-dominated behavior from the macroscopic perspective due to rotation between both roving directions. Mesoscopic effects occurred in the form of limited roving slippage close to the outer contour and isolated gaps as well as mesoscopic wrinkles in highly curved areas. For the highly unbalanced UD-NCF, similar to Task 1, an asymmetrical deformation behavior was also observed during forming. Shear deformation resulted from parallel roving slippage rather than fiber rotation as with Biax-NCF. The lower stiffness in the transverse direction leads to additional tensile and compressive strains, which affected the local fiber volume content due to gapping or in-plane roving compaction. In single-layer tests in particular, gapping occurred due to large tension in the stitching direction or strong in-plane bending of the rovings since shear transverse to the fiber direction is not possible. The in-plane roving compaction is an independent deformation component for UD-NCF and is not caused by shear alone, compared to the behavior of Biax-NCF. The results of Task 3 constitute an extensive database [14] to develop and validate forming simulation approaches for UD- and Biax-NCF, which was not available for UD-NCF in particular yet.
Task 4: Macroscopic forming simulation based on generalized continua
A new 2D macroscopic forming model for UD-NCF based on a modular hyperelastic membrane approach [15] was developed at KIT, because an existing approach [4] was found to be unsuitable for the objectives of the AMECOMP project in an initial numerical evaluation study [16]. The high complexity and number of material parameters of the existing approach [4] would have impeded its transferability to the investigated UD-NCF and the integration of a 2nd gradient approach. In addition, unexpected instabilities were encountered during application to forming with blank holders. The new macroscopic approach [15] introduces a coupling between the transverse tensile and in-plane compressive behavior to account for large roving slippage. The model was parameterized based on the off-axis-tension tests [9] from Task 1. High quantitative agreement was achieved with less than half the necessary material parameters of the existing approach. The modular approach simplifies the parameterization as well as the transferability to new materials as demonstrated by application to the Biax-NCF [10]. An in-plane bending stiffness could not be introduced due to the unplanned time required to develop a completely new approach, instead of the initially planned modification of the existing approach. However, higher accuracy and lower tendency to instabilities could be achieved, with less complexity than the previously existing conventional model. Additionally, a non-local modeling framework was developed [19] for future prediction of localized slippage between adjacent fiber rovings.
A new 3D solid-shell formulation based on methods to avoid numerical locking and with necessary modifications for forming simulation of engineering textiles was developed at KIT [10, 17]. The second displacement gradient over the thickness of the element is calculated based on a Taylor decomposition, to introduce a decoupling of the membrane and bending behavior based on a second gradient approach (out-of-plane). The developed solid-shell element is capable of modeling the forming behavior with a single element over the thickness for large aspect ratios independent of the material model. This increases the numerical efficiency and enables direct transferability of methods developed for 2D approaches.
Task 5: Validation and comparison of conventional and generalized continua approaches
Mesoscopic approach on part level: The forming process of the Biax-NCF is simulated using the mesosopic model for a better understanding of the local effects. Although these simulations require expansive computation costs, they give a reliable and accurate prediction of the local forming defects such as gaping and fiber sliding. They can also be used inversely to design the forming process in such a way that an overall optimal fiber alignment is achieved, and local defects are minimized. The simulation of the forming process is validated through a comparison of the outer contour and shear angles in experimental and simulation results [18]. The stretched and compressed stitches and the change in roving direction can be visualized directly at the meso level. The formation of gapping is analyzed. Large gapping is observed at the corner shape for both the square box and tetrahedron punch shape.
The forming simulation will be extended to UD-NCF in future research, since UD-NCF has significantly larger defects due to the lower stiffness of the stitching.
Macroscopic approach on part level: The macroscopic forming model for UD-NCF (Task 4) is comprehensively evaluated qualitatively and quantitatively based on the experimental forming tests (Task 3). The specific deformation behavior of UD-NCF with an asymmetric deformation in different modes is well predicted in all configurations. The shear and compressive strains are in particular good agreement. Deviations for the transverse tensile strains are observed for two reasons: First, the lack of an in-plane bending stiffness, which is justified in Task 4. Second, a pressure-dependent transverse tensile behavior of the UD-NCF due to local clamping of glass fibers was observed due to the application of blank holders, whose significant impact on the forming was not reported before the onset of the project. The modeling of this effect would require a non-local method, which is not limited to the locally available information within each element, and the combination with the new 3D-solid-shell to propagate the impact of local pressure along the elements in glass-fiber direction. The development of such a non-local framework was started during the AMECOMP project [19] but requires further research. The general transferability of the approach to Biax-NCF [10] was also validated using the forming tests from Task 3. The developed 3D solid-shell element [10, 17] with a membrane-bending decoupling based on a generalized continua approach (Task 4) can model forming processes as accurately as the conventional 2D approaches with the same number of elements, but with the additional prediction of the behavior in thickness direction [10]. This improves the prediction of the local fiber volume content and enables future research concerning the introduction of relevant couplings for multi-axial stress states, which cannot be modeled with 2D approaches.
Task 6: Recycling
Due to difficulties in identifying natural fiber-based NCFs suitable for comparison in this project, and the lack of relevant recycling expertise, following the unexpected health situation of Philippe Boisse, this task was not pursued further.
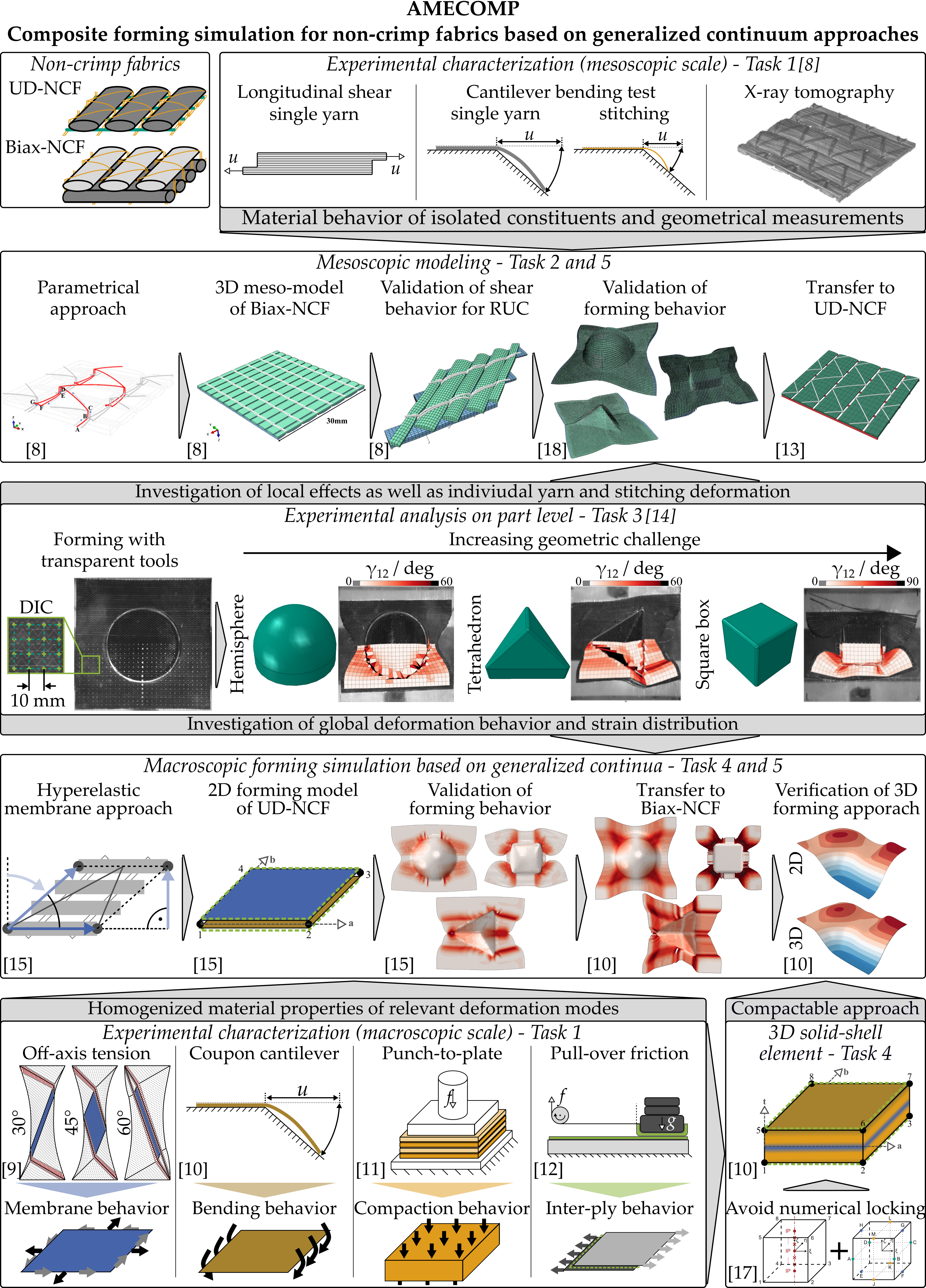
5. Results processing
The results of the project were published in 2 dissertations, 2 scientific papers in international peer-reviewed journals, 2 scientific papers under review in international peer-reviewed journals at the end of the project, and 8 peer-reviewed conference papers with oral presentations at international conferences, and 1 conference paper (non-peer-reviewed) with oral presentation at an international conference. The developed solid-shell element will be further used and enhanced within the „AI Research Unit 5339“, funded by DFG. The macroscopic approach for UD-NCF is used and enhanced in LuFo research project Electra (20W1912D), funded by the German Federal Ministry for Economic Affairs and Climate Action (BMWK). All developments of the macroscopic approaches (Task 4) will be used in industrial applications as part of license agreements of KIT, for example with the KIT start-up Simutence GmbH.
6. Discussion
This project faced several difficulties. Firstly, the project began with the start of the covid crisis, which made it difficult to get off the ground. In addition, after two years of the project, the French coordinator Philippe Boisse was, unfortunately, no longer able to support the project due to serious health problems. This hampered, but did not prevent the partners from exchanging and moving forward hand in hand.
The objectives of the experimental investigations for characterization (Task 1) and forming behavior (Task 3) of UD and Biax-NCF were successfully achieved. They form a comprehensive database within the project and for future research, and fill relevant research gaps in the knowledge of NCFs. The objective to develop a mesoscopic modeling approach for Biax-NCF (Task 2) suitable for studying local effects during forming (gapping) and, in principle, for virtual material characterization has also been achieved. The application of generalized continua approaches for mesoscopic models was not further investigated, as the alternatively developed embedded beam approach was found to be sufficient and computationally advantageous. Future work could focus on validating the approach for UD-NCF as well as explicitly conducting virtual material characterization to parameterize macroscopic approaches or to replace experimental tests for different NCF architectures.
The objectives related to the macroscopic forming simulation have been partially achieved. It turned out that existing membrane modeling approaches for NCF were not suitable as foundation for the development of generalized continuum mechanics approaches. Thus, the additional effort to develop a new model prevented the investigation of the in-plane bending stiffness of the rovings. Nevertheless, the new membrane approach (Task 4) can describe the behavior more accurately than the existing approach with a significantly reduced numerical complexity, which increases the transferability to other textile materials. For the out-of-plane bending stiffness, generalized continua approaches have been successfully used to model the forming behavior with a compactable 3D solid shell. The experimental observations and validation in Task 5 indicate that it will be necessary to model in-plane bending stiffness in the future. This could be combined with the identified need for a non-local approach to improve modeling the pressure-dependent transverse behavior and roving slippage.
7. Conclusions
The AMECOMP project successfully initiated a German-French cooperation between KIT and INSA Lyon. Both research groups continuously exchanged their knowledge and results to improve the understanding of non-crimp fabrics. The project has provided training to several young scientists and the results have been published in scientific journals as a contribution to the openly available state of research and discussed with other scientists in the same field at several conferences. The experimental results of the project led to a better understanding of the mechanisms involved for all macroscopic and mesoscopic deformation modes as well as the overall forming behavior. The developed numerical approaches achieve high accuracy at the mesoscopic and macroscopic scales for this challenging class of materials. The reliable methods of this project can be used to better exploit the enormous potential of NCFs for lightweight construction, improving both performance and environmental impact. Development using methods based on generalized continuum mechanics and non-local approaches should be further pursued in the future, to account for microscopic and mesoscopic effects even more accurately at the next larger scale.
8. References
[1] P. Boisse, R. Akkerman, P. Carlone, L. Kärger, S. V. Lomov, and J. A. Sherwood, Advances in composite forming through 25 years of ESAFORM, International Journal of Material Forming, 15(3), 2022, DOI: 10.1007/s12289-022-01682-8.
[2] J. Sirtautas, A. K. Pickett, and P. Lépicier, A mesoscopic model for coupled drape-infusion simulation of biaxial Non-Crimp Fabric, Composites Part B: Engineering, 47, pp. 48–57, 2013, DOI: 10.1016/j.compositesb.2012.09.088.
[3] T. Senner, S. Kreissl, M. Merklein, J. Meinhardt, and A. Lipp, A modular modeling approach for describing the in-plane forming behavior of unidirectional non-crimp-fabrics, Production Engineering, 8(5), pp. 635–643, 2014, doi: 10.1007/s11740-014-0561-z.
[4] F. J. Schirmaier, D. Dörr, F. Henning, and L. Kärger. A macroscopic approach to simulate the forming behaviour of stitched unidirectional non-crimp fabrics (UDNCF). Composites Part A: Applied Science and Manufacturing, 102, pp .322–335, 2017. DOI: 10.1016/j.compositesa.2017.08.009
[5] H. Xiong, E. Guzman Maldonado, N. Hamila, and P. Boisse. A prismatic solid-shell finite element based on a DKT approach with efficient calculation of through the thickness deformation. Finite Elements in Analysis and Design, 151, pp. 18–33, 2018.
[6] P. Boisse, N. Hamila, and A. Madeo. The difficulties in modeling the mechanical behavior of textile composite reinforcements with standard continuum mechanics of Cauchy. Some possible remedies. International Journal of Solids and Structures, 154, pp. 55–65, 2018.
[7] P. Boisse, J. Colmars, N. Hamila, N. Naouar, and Q. Steer. Bending and wrinkling of composite fiber preforms and prepregs. A review and new developments in the draping simulations. Composites Part B: Engineering, 141, pp.234–249, 2018.
[8] R. Zheng, N. Naouar, J. Colmars, A. Platzer, B. Schäfer, F. Morestin, L. Kärger, Philippe Boisse. Mesoscopic finite element modeling of biaxial non-crimp fabric including representative stitch pattern. Composite Structures, 2024, DOI: 10.1016/j.compstruct.2024.118126
[9] B. Schäfer, R. Zheng, N. Naouar, and L. Kärger. Membrane behavior of uni- and bidirectional non-crimp fabrics in off-axis-tension tests. International Journal of Material Forming, 16(6):Art. 68, 2023, DOI: 10.1007/s12289-023-01792-x.
[10] B. Schäfer. Macroscopic forming simulation of unidirectional non-crimp fabrics: Hyperelastic material modeling and 3D-solid-shell approach, Dissertation, Karlsruhe Institute of Technology, Karlsruhe, Germany, 2024.
[11] B. Schäfer, R. Zheng, P. Boisse, and L. Kärger. Investigation of the compaction behavior of uni- and bidirectional non-crimp fabrics. Materials Research Proceedings, 28, pp. 331–338, 2023, DOI: 10.21741/9781644902479-36.
[12] B. Schäfer, R. Zheng, N. Naouar, and L. Kärger. Investigation of the friction behavior of uni- and bidirectional non-crimp fabrics. Materials Research Proceedings, 41, pp. 540-548, 2024, DOI: 10.21741/9781644903131-60
[13] A. Hitter. Mesoskopische Modellierung des Deformationsverhaltens von unidirektionalen Kohlenstofffaser-Gelegen (UD-NCF). Bachelor’s thesis, KIT, 2022
[14] B. Schäfer, R. Zheng, J. Colmars, A. Platzer, N. Naouar, P. Boisse, L. Kärger. Experimental analysis of the forming behavior of uni- and bidirectional non-crimp fabrics for different geometries. [submitted for review]
[15] B. Schäfer, D. Dörr, R. Zheng, N. Naouar, and L. Kärger. A hyperelastic approach for modeling the membrane behavior in finite element forming simulation of unidirectional non-crimp fabrics (UD-NCF). [submitted for review]
[16] B. Schäfer, S. Haas, P. Boisse, and L. Kärger. Investigation of the Membrane Behavior of UD-NCF in Macroscopic Forming Simulations. Key Engineering Materials, 926, pp. 1413–1422, 2022, DOI: 10.4028/p-2977b4.
[17] B. Schäfer, D. Dörr, and L. Kärger. Potential and challenges of a solid-shell element for the macroscopic forming simulation of engineering textiles. PoPuPS of ULiège Library, 2021, DOI: 10.25518/esaform21.883.
[18] R. Zheng. Simulation de la mise en forme de renforts NCF de composites basée sur des approaches mesoscopiques, Dissertation, Institut national des sciences appliquées de Lyon, Lyon, France, December 2023.
[19] J. P. Wank, B. Schäfer, J. Mitsch, and L. Kärger. Strain gradient calculation as a basis for localized roving slip prediction in macroscopic forming simulation of non-crimp fabrics. Materials Research Proceedings, 41, pp. 467-476, 2024, DOI: 10.21741/9781644903131-52.
List of publications during the project
International peer-reviewed Journals
Multi-partner publications
- B. Schäfer, R. Zheng, J. Colmars, A. Platzer, N. Naouar, P. Boisse, L. Kärger. Effect of the component geometry on the forming behavior of uni- and bidirectional non-crimp fabrics. [submitted for review]
- B. Schäfer, D. Dörr, R. Zheng, N. Naouar, and L. Kärger. A hyperelastic approach for modeling the membrane behavior in finite element forming simulation of unidirectional non-crimp fabrics (UD-NCF). [submitted for review]
- R. Zheng, N. Naouar, J. Colmars, A. Platzer, B. Schäfer, F. Morestin, L. Kärger, Philippe Boisse. Mesoscopic finite element modeling of biaxial non-crimp fabric including repre-sentative stitch pattern. Composite Structures, 2024, DOI: 10.1016/j.compstruct.2024.118126
- B. Schäfer, R. Zheng, N. Naouar, and L. Kärger. Membrane behavior of uni- and bidirec-tional non-crimp fabrics in off-axis-tension tests. International Journal of Material Forming, 16(6):Art. 68, 2023, DOI: 10.1007/s12289-023-01792-x.
International communications (conference) with publication of peer-reviewed conference papers
Multi-partner publications
- B. Schäfer, R. Zheng, N. Naouar, and L. Kärger. Investigation of the friction behavior of uni- and bidirectional non-crimp fabrics. Materials Research Proceedings, 41, pp. 540-548, 2024, DOI: 10.21741/9781644903131-60
- R. Zheng, N. Naouar, B. Schäfer, A. Platzer, J. Colmars, L. Kärger, and P. Boisse. Draping of biaxial non-crimp fabric on hemispherical shape. Materials Research Proceedings, 41: pp. 623-630, 2024, DOI: 10.21741/9781644903131-69
- B. Schäfer, R. Zheng, P. Boisse, and L. Kärger. Investigation of the compaction behavior of uni- and bidirectional non-crimp fabrics. Materials Research Proceedings, 28:pp. 331–338, 2023, DOI: 10.21741/9781644902479-36.
- R. Zheng, B. Schäfer, A. Platzer, J. Colmars, N. Naouar, and P. Boisse. A unit-cell mesoscale modelling of biaxial non-crimp-fabric based on a hyperelastic approach. Materials Research Proceedings. 28:pp. 285–292, 2023, DOI: 10.21741/9781644902479-31.
- B. Schäfer, S. Haas, P. Boisse, and L. Kärger. Investigation of the Membrane Behavior of UD-NCF in Macroscopic Forming Simulations. Key Engineering Materials, 926:pp. 1413–1422, 2022, DOI: 10.4028/p-2977b4.
Single-partner publications
- J. P. Wank, B. Schäfer, J. Mitsch, and L. Kärger. Strain gradient calculation as a basis for localized roving slip prediction in macroscopic forming simulation of non-crimp fabrics. Materials Research Proceedings, 41, pp. 467-476, 2024, DOI: 10.21741/9781644903131-52
- B. Schäfer, D. Dörr, and L. Kärger. Potential and challenges of a solid-shell element for the macroscopic forming simulation of engineering textiles. PoPuPS of ULiège Library, 2021, DOI: 10.25518/esaform21.883.
- L. Kärger, S. Galkin, E. Kunze, M. Gude, and B. Schäfer. Prediction of forming effects in UD-NCF by macroscopic forming simulation – Capabilities and limitations. PoPuPS of ULiège Library, 2021, DOI: 10.25518/esaform21.355
International communications (conference) with publication of conference papers
Multi-partner publications
- R. Zheng, B. Schäfer, N. Naouar, J. Colmars, A. Platzer, P. Boisse. Analysis of the in-plane shear behavior of biaxial non-crimp-fabric at mesoscopic scale. Proceedings of the 2023 International Conference on Composite Materials, Belfast, 30th July - 4th August 2023, Queen’s University Belfast (https://www.iccm-central.org/Proceedings/ICCM23proceedings/papers/ICCM23_Full_Paper_209.pdf)
National publications in France or Germany
- R. Zheng. Simulation de la mise en forme de renforts NCF de composites basée sur des approaches mesoscopiques, Dissertation, Institut national des sciences appliquées de Lyon, Lyon, France, December 2023.
- B. Schäfer. Macroscopic forming simulation of unidirectional non-crimp fabrics: Hyperelastic material modeling and 3D-solid-shell approach, Dissertation, Karlsruhe Institute of Technology, Karlsruhe, Germany, March 2024. https://doi.org/10.5445/IR/1000170739