EcoDynamic SMC
- Contact:
- Funding:
BMWi
- Partner:
KIT-FAST, Fraunhofer ICT, KIT-IAM, Autotech Engineering Deutschland GmbH, DG Flugzeugbau GmbH, KOLLER Formenbau GmbH, Schmidt & Heinzmann GmbH & Co. KG, Toray Industries Europe GmbH, Vibracoustic SE & Co. KG, BMW Group, Premium AEROTEC GmbH, Simutence GmbH
- Startdate:
October 2021
- Enddate:
September 2024
Economical, dynamically stressed, durable and resource-efficient CF-SMC components for large-scale production
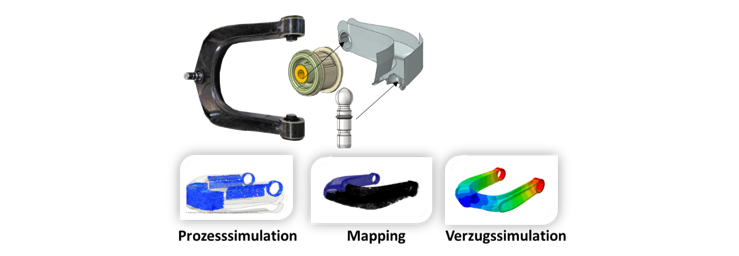
Lightweight design and materials are effective tools for reducing CO2 emissions in the use phase of vehicles. In the course of the advancing trend towards e-mobility, lightweight design plays a key role in improving energy efficiency. In this context, the substitution of metallic materials with fibre-reinforced plastics has many useful advantages. Carbon fibre-reinforced SMC lends itself to the production of structural lightweight components due to its outstanding weight-specific properties combined with the productivity of the process, as well as the potential for a high degree of functional integration. Despite the positive material and shaping properties of the SMC process, however, no SMC fibre composite component has yet been used in large-scale production in the chassis of a vehicle or the primary structure of an aerospace application. Reasons for this are the insufficient predictability of the semi-finished product quality, the component properties and the long-term behaviour. Following the overall project goal of developing CF-SMC technology for the production of dynamically loaded, safety-relevant components for large-scale series application, the process-related challenges are to be researched and overcome in Eco-Dynamic-SMC. This requires the consideration of the complete SMC process chain, including the virtual counterpart with the linked process and structure simulation. These approaches will be demonstrated using two components, one is suspension control arm and other is Motor glider landing gear component.
The KIT-FAST is responsible for process and structure simulation in the project. The first transfer of a continuous, virtual process chain for impact extrusion processes of CF-SMC semi-finished products from research to industrial application will shorten the development time and enable resource-efficient component design. The implementation of this virtual process chain requires the definition of suitable interfaces for data transfer between the individual sub-steps of the process and structure simulation. Furthermore, KIT-FAST will extend the existing models of the process simulation to consider the effects of curing and cooling of the resin system, or the composite, and to consider the associated residual stresses or warpage.